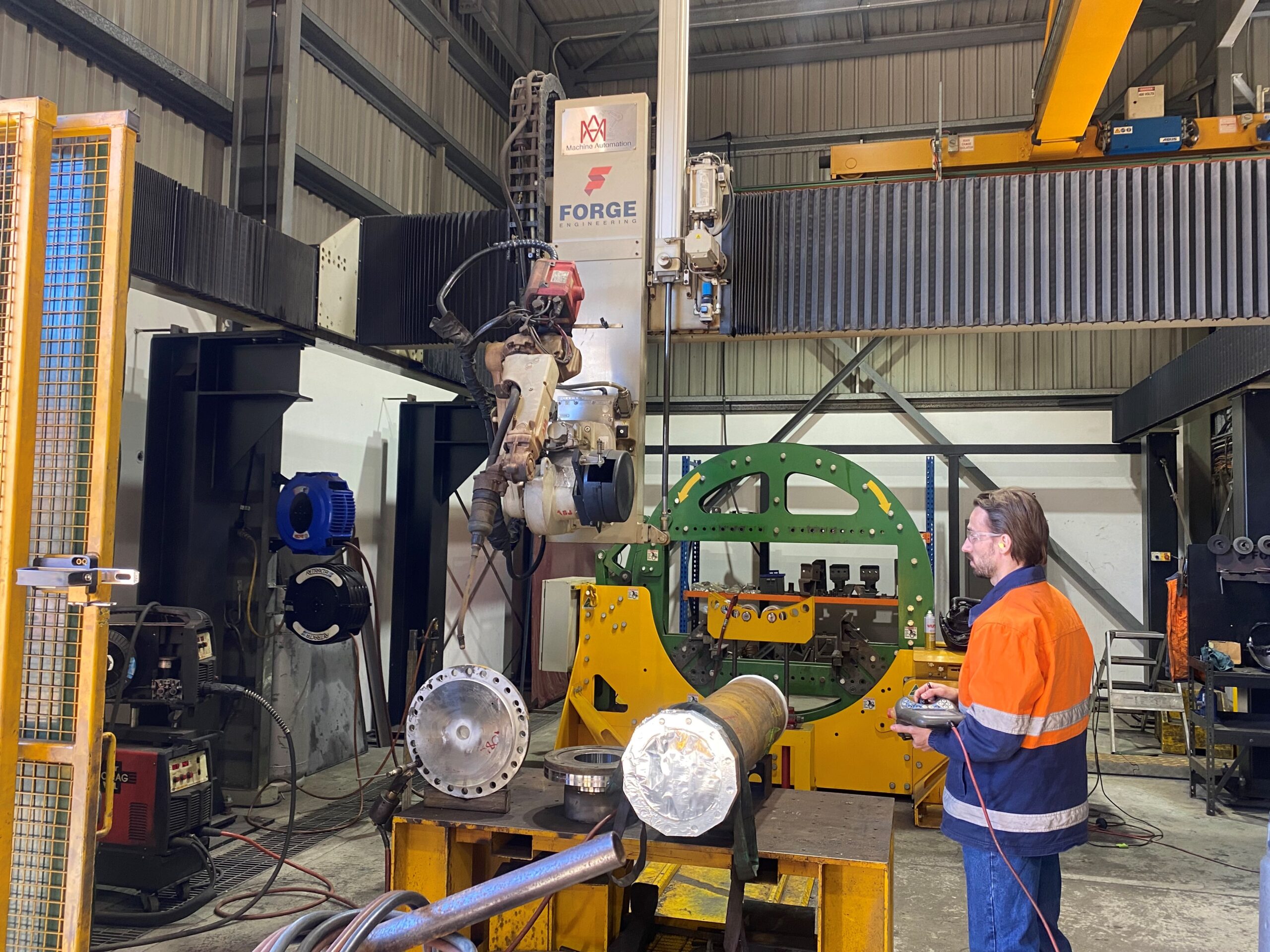
Bots of possibilities forge towards workforce transformation.
Utilising modern technology for smarter solutions in their workshop – circuit by circuit they are powering a new era of human-robot collaboration. Programmer and Draftsman Harry Parker believes Forge Engineering is at the forefront of innovation, pushing the boundaries of what is possible and unlocking new ways of working.
Harry emphasises the importance of human expertise in robotics, highlighting the symbiotic relationship between skilled professionals and advanced technology. He said this perspective is pivotal as we transition through Industry 4.0 and look towards Industry 5.0.
“I want to help bring people into the industry 4.0 and eventually 5.0 transformation and upskill the local workforce.”
Three of their boilermakers have already been trained to use the welding robot and opportunity, Harry believes they may not have had otherwise.
“I think I’d like to foster an environment where people really feel like they can have their input heard. “That’s really part of it, that transformation must involve everyone. “There has to be buy in from everyone, and I’d like to be in a workplace that that allows it – that’s certainly been the case with the robot so far,” Harry said.
Part of Forge’s workplace culture is you can’t be what you can’t see, and it is this philosophy that leads to showing the next generation the types of jobs available. Harry said Forge takes part in five school tours a year, as well as work experience students and apprenticeships.
“We typically have about five school tours a year, so we take large groups. It’ll usually be a whole classroom, and we’ll split them up into smaller tours and just move around the workshop. “They go through everything, including our manual machines, which is probably what they’re a bit more familiar with, and then move on to the CNC, machines which are automated, and then to the welding robot. I think trying to get more people in the door to have a look and see what we do really is, is the big thing. The variety that we have here makes it quite interesting. It’s a different thing every day.”
So, what is Harry’s advice for the future engineers, diesel fitters and boilermakers? “Just don’t be afraid to make mistakes. I certainly felt when I left university, like I knew everything. I quickly realised I knew very little. Having the humility to just accept that there are people out there who know a lot more than you and that that can be valuable.”
If we didn’t have skilled people, that would be a big challenge. “You can’t just place a robot where there hasn’t been a person before to teach it,” Harry said.
Watch the Greater Foundations presentation video
Find out more about Forge Engineering here: https://forgeengineering.com.au/
Latest News
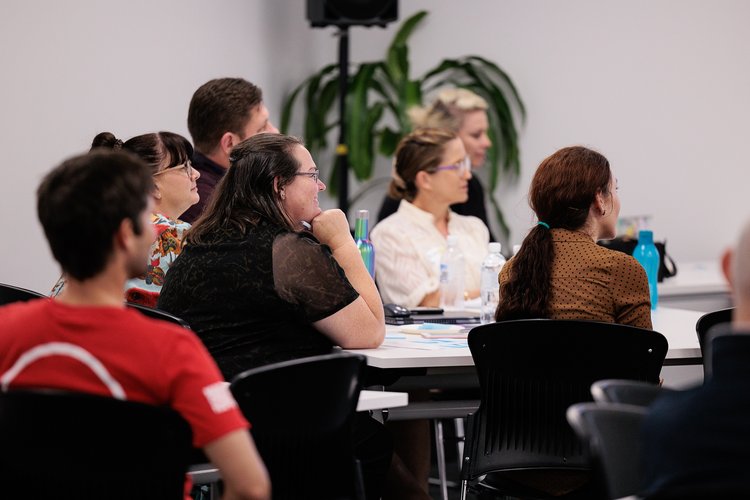
Greater Foundations24 set to empower educators to unlock greater career possibilities
Greater Whitsunday Alliance (GW3) is again delivering the Greater Foundations program, aimed at informing Greater Whitsunday teachers and educators on what career and workforce opportunities exist across the region.
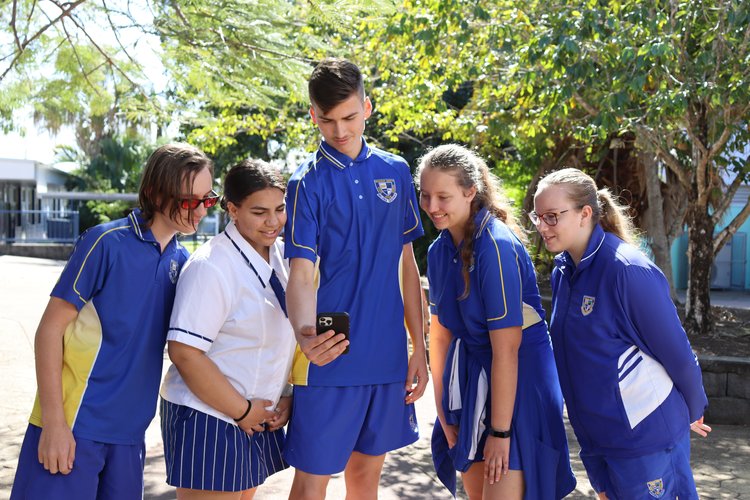
Career education modules showcase opportunities across the Greater Whitsunday region
Greater Whitsunday Alliance (GW3) is leading a regional approach to education, skills, and training with the launch of the For Greater Careers Education Program
Featured Programs
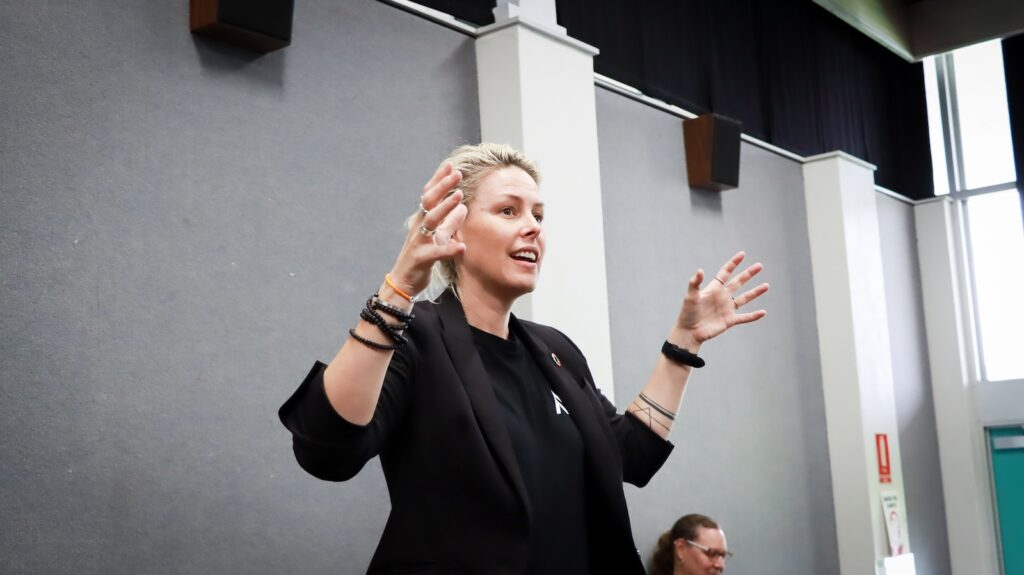
Greater Foundations
Greater Whitsunday Alliance (GW3) are building career-based classroom learning with Greater Foundations, a professional development event for educators across the Greater Whitsunday region.